Designing Storage Racks Layout to Improve Warehouse Efficiency
Warehouses are not just storage spaces but critical components of businesses. The racking system design and operations layout of your warehouse can greatly boost the efficiency, speed of logistics operations and ultimately, improve customer satisfaction.
If you are building your warehouse from the scratch, you need to collaborate not just with the architects and the construction teams, but also with the warehouse managers and supervisors of your operations for real-time insights into the needs of the workflow. Let us take a closer look at the features that can make or break the design and functionality of your warehouse.
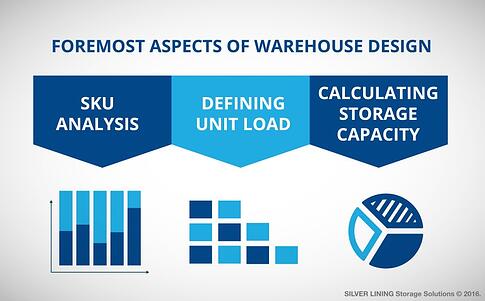
1.1 Warehouse Design Aspects
The foremost aspects of warehouse storage racks design that should be considered on a high priority are the following:
- SKU Analysis: You can sort SKUs into different categories depending on their shape, size, weight, and the rate of movement of the SKU. Some SKUs contribute more to total sales than others. The 80/20 rule – 20% of SKUs usually account for 80% of unit sales: These SKUs should be placed in a “Hot Pick” zone to grab the attention of the distribution center staff for most efficient processing.
- Defining Unit Load: Depending upon the type (two-way, four-way, reversible, irreversible) and size of pallets (Euro, Industrial) – used in your other warehouses, the unit load has to be defined and standardized.
- Calculating Storage Capacity: The potential storage space – vertical plus individual space of the distribution center should be utilized to the maximum potential. Cubic capacity of the vertical space as well as individual location must be exploited optimally. Ensure maximization of cube level and ground level square footage. Storage capacity should be worked out on the basis of whether you need Fixed Location, Random Location, or Mixed Storage systems.
Once the above aspects have been considered, next you should focus on the way the operations inside the warehouse take place. The following criteria will also determine the ideal layout of a warehouse:
- Estimating Throughput Levels: Calculation of the safe productivity for each loading bay based on peak day stock movement gives an estimate of the warehouse daily throughput.
- Nature of Products: Space design of the warehouse majorly depends upon the type of products stored – inflammable, frozen, perishable or pharmaceutical.
- Storage, Retrieval and Location Control System: These three activities form the backbone of the operations. Fast-moving goods should be near the dispatch areas while slow-moving SKUs should be towards the back of the warehouse. Ensure a dynamic, ongoing slotting process.
- Flexibility in the Racking Layout and Operations: Planning for unforeseen changes to the business or fulfillment model is necessary to avoid high costs for unplanned changes to the facility and operations. It is imperative to develop flexible, scalable storage racking layouts. It should enable minimum handling of products and also minimize congestion and interference areas to ensure smooth flow.
- Provide Adequate Space on Docks: Insufficient space at docks causes inefficiencies in the dock operations and can adversely affect other functions. Having enough dock doors and adequate space at the docks streamlines process. It also helps in cross-docking.
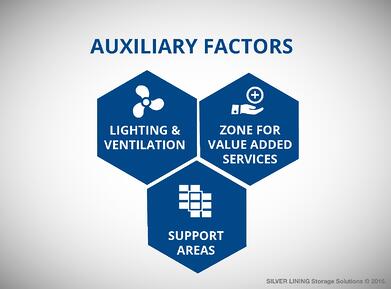
1.2 Auxiliary Factors of Warehouse Design
Finally, the below factors should also be considered. Other than the operations-critical spaces, these auxiliary spaces also play a role in the efficient working of your warehouse.
A. Lighting and Ventilation: Warehouse design should consider availability of enough natural and artificial light, as well good ventilation. The positions of ceiling lights need to be finalized keep in mind the storage layout.
B. Zone for value added services: Specific area need to earmarked for value added services such as bulk breaking, kitting, invoicing, special gift-wrapping or adding promotional materials to packaging prior to shipping etc.
C. Support Areas: Apart from the core storage, auxiliary areas such as receiving/dispatch docks, office facilities, safety equipment area, parking, etc. are also crucial in a warehouse and should be factored into the blueprint. The minimum, maximum, and optimum depths of the dock and the position and size of offices have to be determined in order for efficient space utilization.
Conclusion
Planning and designing a warehouse is a complex and intricate process that involves not just the above principles but also many other small but significant factors. An efficient and intelligent design can be put in place by envisioning maximum possible scenarios and requirements, and planning solutions for each of them.
For more insights and to have an intelligent storage and operation layout in your warehouse or distribution center, please write to us at sales@silverliningstorage.in
We will be happy to resolve your storage and material handling challenges.
Thank you for reading our post. If you would like to read our regular posts, get ideas, tips, hacks ‘Follow us on Linkedin ‘.
Topics: warehouse storage layout design, racking layout, warehouse design, warehouse operations design, warehouse layout